近年来,中国的零部件制造企业的水平不断提升,推广了主机配套进行滚动交付的模式,对零部件企业的配套协同性和及时性要求也相应增强。在国家倡导强链、补链、稳链的政策引导下,企业的运营稳定性和可持续性变得非常重要。面向核心链主的供给模式却仍依赖滚动预测驱动,如何平衡链主的准时交付要求和自身备库水平成为企业管理面临的难题。
嘉兴某企业如何应对频繁变动的预测需求挑战,实现准时交付与备库平衡?
嘉兴某企业专注于生产和销售电子五金、电气五金、电器五金、服饰五金、箱包扣具、家具五金等各种五金配件及组合件。拥有的生产工艺包括冲压、热处理、表面处理、委外电镀等,其原材料采用钢、铁、铜等大宗期货商品,但其配套的客户提出的预测需求频繁变动,给企业管理准时交付和备库水平带来了极高的挑战。
该客户在预测管理中面临的难题如下:
1、无法及时响应客户需求的生产计划:由于预测变更频繁,目前需要通过手工处理和分析来完成,工作量大且耗时长,每次新的预测处理都需要耗费两天的时间。
2、缺乏专业的分析工具:没有适用于预测波动分析的专业工具,需要人工清洗和分析数据,容易出现手工失误。
如果客户需求发生变更,后续的生产计划和采购计划无法立即响应并进行相关调整,就会导致库存过高和缺货共存的情况。高库存会占用厂内资金,影响企业运营,而缺货则会降低客户满意度。
面对以上难题,预测透镜根据其行业特点和用户痛点,提供了一套解决方案,帮助该企业实现了生产计划的自动化处理。
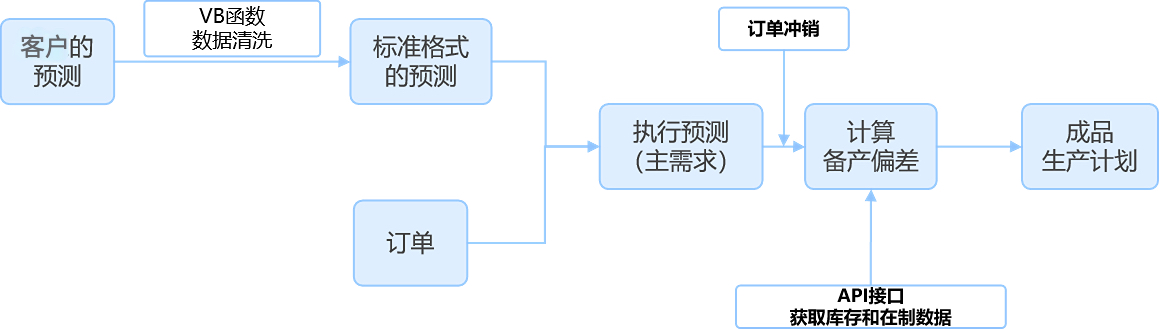
1. 通过VB函数方式处理不规范的原始客户预测数据。
2. 使用知识中台,智能识别导入预测的样式,并支持行列数据转换。
3. 利用数据驱动和自动侦测技术,当检测到客户预测和订单数据更新时,自动截取备产需求,并按订单冲销规则进行冲销,形成可执行的预测计划。
4. 自动获取ERP系统中对应品号的库存和在制数据,完成备产偏差分析。
5. 将分析结果发送给相应的责任人,选择相应的成品生产计划处理方案。
这样,客户不再需要手工进行数据清洗、跨系统数据捞取清洗,以及多个Excel多函数的分析。全过程应用自动化,实现数据驱动,减少了人工处理的工作量,降低人工失误率。同时,可以快速响应预测需求变动,及时纠偏,减少对库存和交付的影响。
预测透镜为嘉兴某企业带来了切实的价值效应,降低了预测导致的呆滞比例,降低了库存周转天数,提升了客户预测能力,提高了预测响应能力,也提高了预测出货达成率,实现了准时交付与备库平衡。