新产品样件试制是产品开发过程中的关键阶段,它涉及从设计概念到物理原型的转换,以验证设计的可行性、功能性以及生产过程的可制造性。在这个过程中,可能会遇到多种问题,以下是一些常见的新产品样件试制问题汇总:
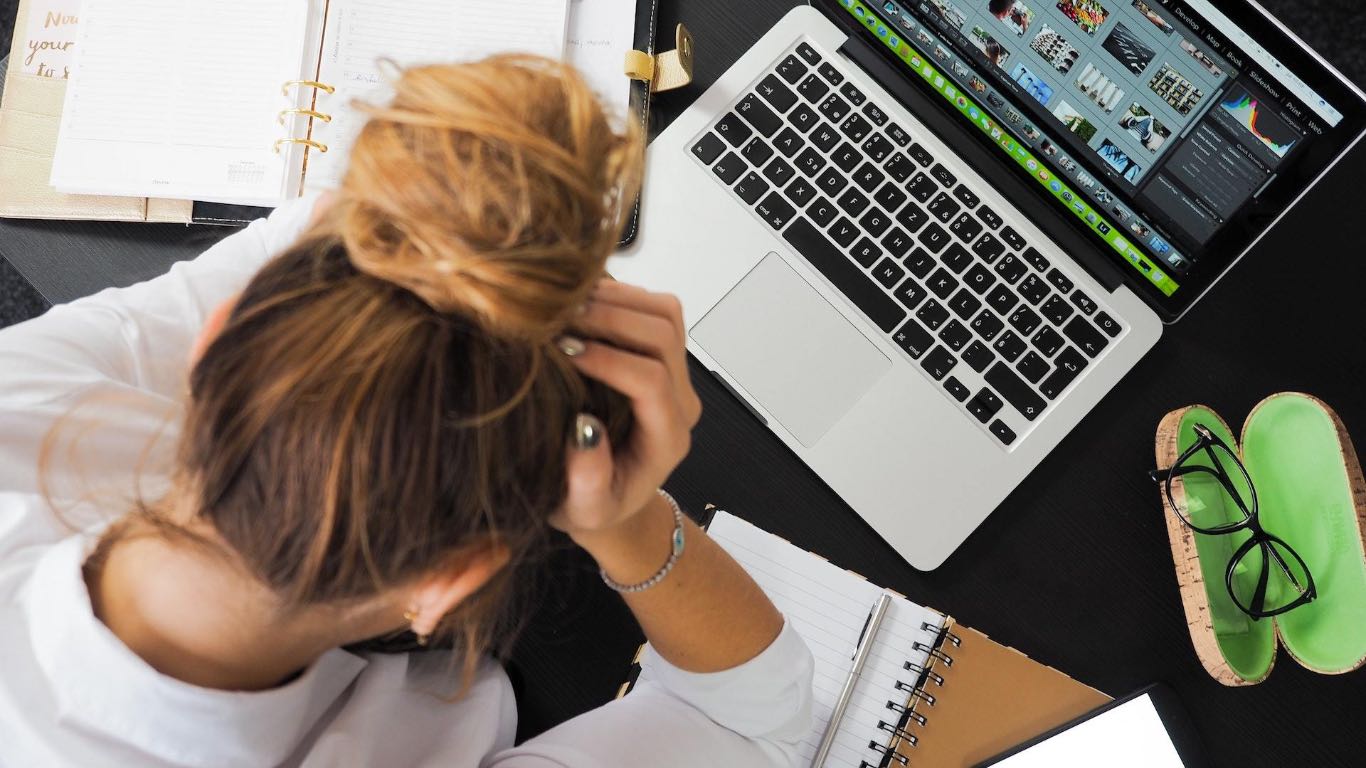
1、设计缺陷:
尺寸误差:CAD模型与实际零件尺寸不符。
结构强度不足:样件在测试中容易损坏或变形。
功能不匹配:样件未能实现预期功能或性能指标。
2、材料选择:
材料属性不符:所选材料的硬度、韧性、耐热性等属性不符合设计要求。
成本过高:选用的材料成本超出预算。
3、加工工艺问题:
加工精度不足:加工设备或工艺导致零件精度低,影响装配。
加工难度大:复杂形状或精细特征的加工难以实现。
表面处理问题:涂层、电镀等表面处理效果不佳。
4、组装问题:
零件配合不良:部件间配合尺寸错误,导致装配困难。
组装顺序不合理:缺乏明确的组装指导,造成组装错误。
紧固件问题:螺钉、销钉等紧固件的规格或数量不合适。
5、测试与验证:
测试条件不准确:实验室环境与实际使用环境差异大。
缺乏适当的测试方法:没有合适的测试标准或流程来评估性能。
数据分析不当:测试数据解读错误,未能正确反映样件性能。
6、成本与时间控制:
超预算:样件试制过程中的意外成本超出预期。
时间延误:供应链问题、设计返工等导致项目延期。
7、法规与标准合规:
安全标准不符:样件未能满足行业安全标准。
法规遵从性问题:设计违反了某些地区的法规要求。
8、知识产权保护:
设计侵权风险:样件设计可能无意中侵犯了他人的专利或版权。
保密协议:与供应商或合作伙伴的保密协议可能未得到妥善处理。
9、供应链与物流:
供应商问题:原材料或零部件供应不稳定。
物流延误:运输或配送过程中出现问题。
10、市场反馈:
用户体验不佳:样件在用户体验测试中收到负面反馈。
市场定位不准确:产品特性与目标市场的需求不匹配。
针对这些问题,开发团队需要进行细致的规划,包括详细的设计审查、材料测试、工艺优化、成本效益分析以及与供应商的紧密合作。同时,建立一个灵活的反馈和修正机制,以便在试制过程中快速识别和解决问题,确保样件能够顺利过渡到批量生产阶段。