在机加工领域,关键工序控制是确保产品质量和生产效率的重要环节。通过对机加工中的关键工序进行严格控制,可以提高产品的准确度、稳定性和可靠性,同时有效控制生产过程的风险和资源的浪费。本文将详细介绍机加工关键工序控制的三个关键步骤。
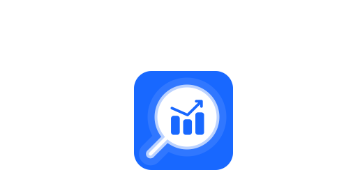
一、工艺规划与制定
在此阶段,制造工程师需要根据产品要求和机加工工艺的特点,制定合理的加工工艺流程。工艺规划应包括材料选择、加工工序的顺序安排、加工设备的选择和刀具的选用等内容。同时,制定详细的工艺图纸和工艺文件,明确每个关键工序的加工参数和要求。
二、设备保养与维护
设备保养与维护是机加工关键工序控制中的重要环节。设备的正常运行对于工序的控制和产品质量的保证至关重要。因此,必须定期进行设备的保养和维护工作,保证设备在工作状态下运行。这包括定期更换润滑油、清洁设备、检查设备的关键部件和传感器的功能是否正常等。
三、质量检验与控制
质量检验与控制是机加工关键工序控制的后一步。在此阶段,应对关键工序加工过程中的产品进行严格的质量检验。质量检验方法可以包括尺寸测量、外观检查、材料成分分析等。对不合格产品应及时进行返工或剔除,以保证关键工序加工的产品达到质量要求。在质量控制方面,应建立质量控制指标和流程,并进行稽核记录。
机加工关键工序控制对于产品质量和生产效率具有重要意义。工艺规划与制定、设备保养与维护、质量检验与控制是机加工关键工序控制的三个关键步骤。企业应注重制定合理的加工工艺流程,保持设备的正常运行状态,严格执行质量检验与控制,以提高产品的准确度、稳定性和可靠性。